Develop Processes to Increase Efficiency, Quality, Safety, & Profitability
Do these challenges sound familiar?
Your team is barely keeping up with orders.
Your product quality is inconsistent.
You are looking for a way to cut down on manual tasks.
You want to improve operational performance.
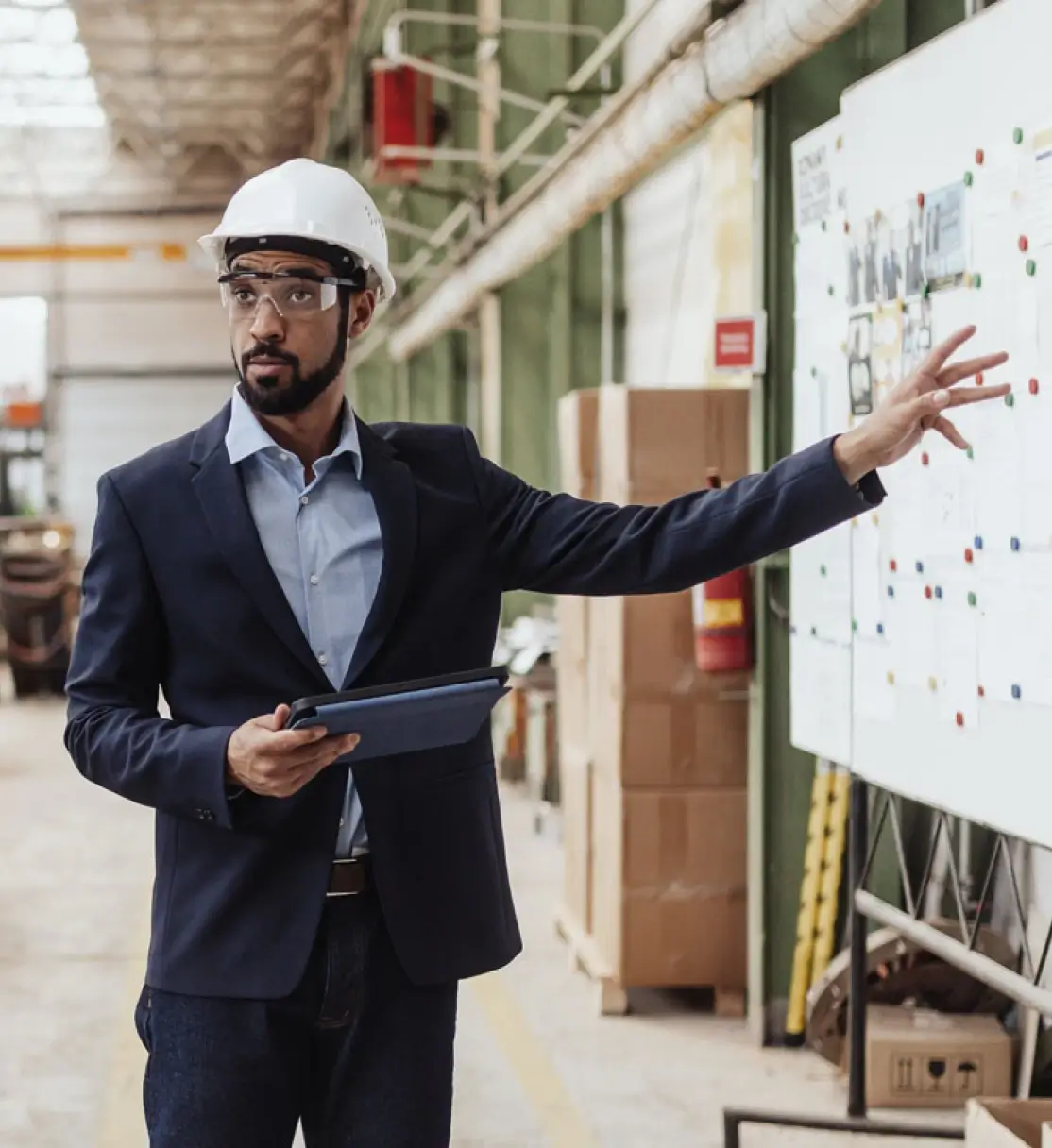
Trusted by Hundreds of Manufacturers Across Nevada
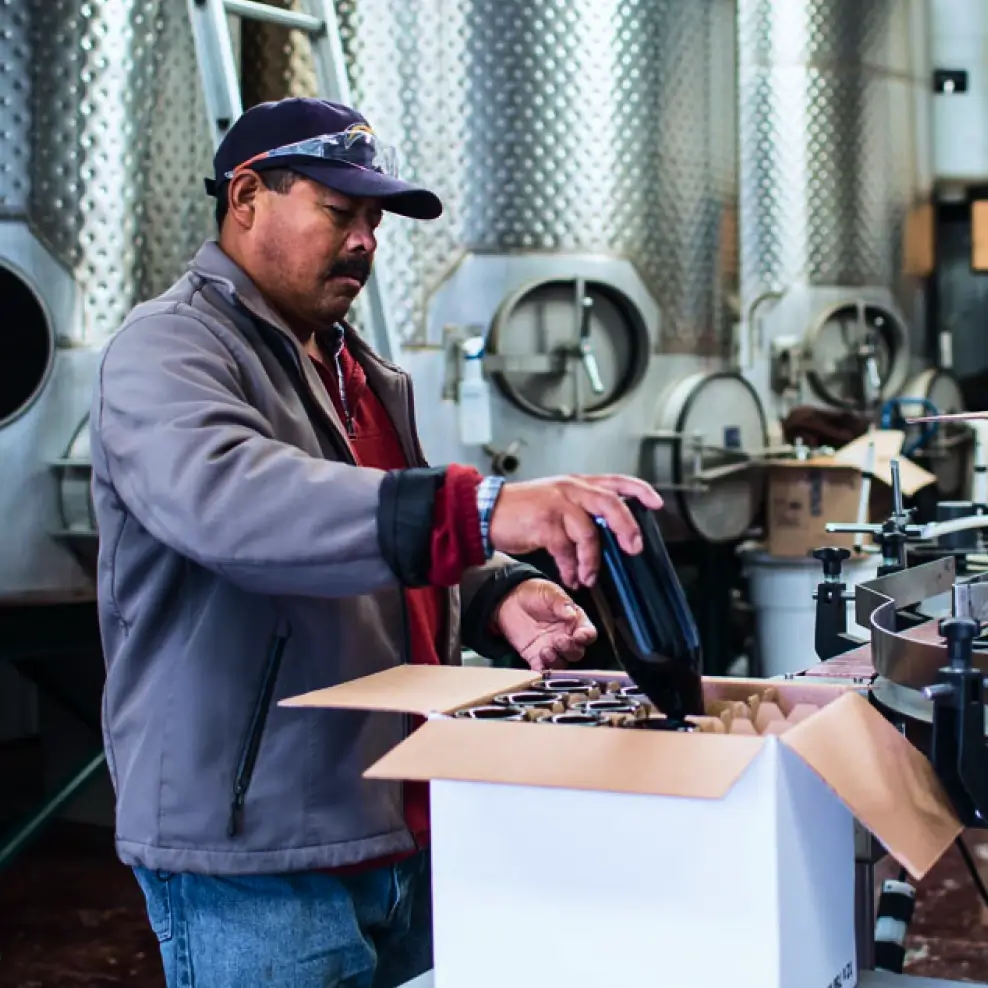
Reduce Waste & Ship More Product
The more efficient your processes, the more units you can sell. We come alongside manufacturers like you to eliminate waste and improve productivity on the line – increasing profitability and customer satisfaction.
“Training has already dramatically reduced rework and waste, lowered residual inventory and helped drive design changes as a result of taking quick action on the line when problems are found.”
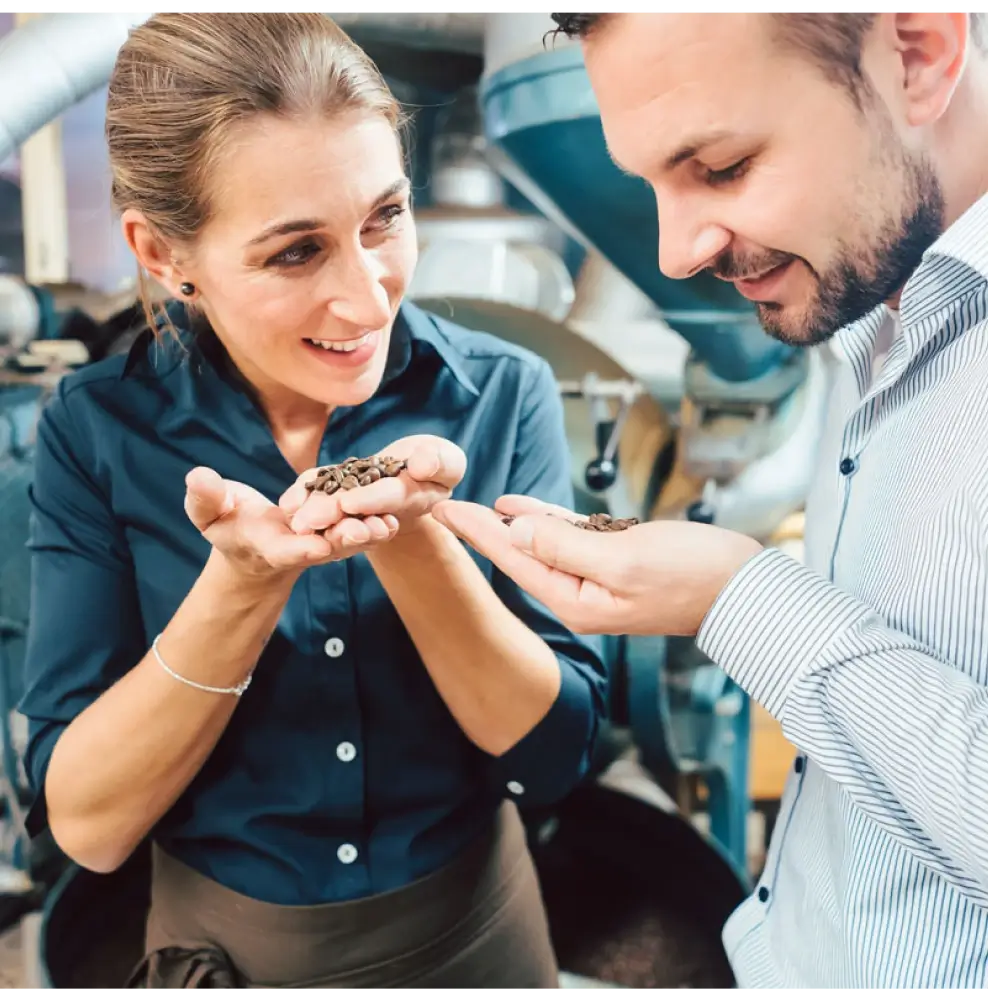
Meet Client Expectations
Increasing the quality management of your production line reduces rejection rate and wasted time. Let us help you keep client satisfaction high by meeting your deadlines with a superior product.
“Having access to the Manufacture Nevada team was a godsend for us. We are now much more cognizant of the quality factors and how we resolve problems. Now, when we identify a problem, we follow the process to document it towards resolution. This allows us to resolve problems quicker.”
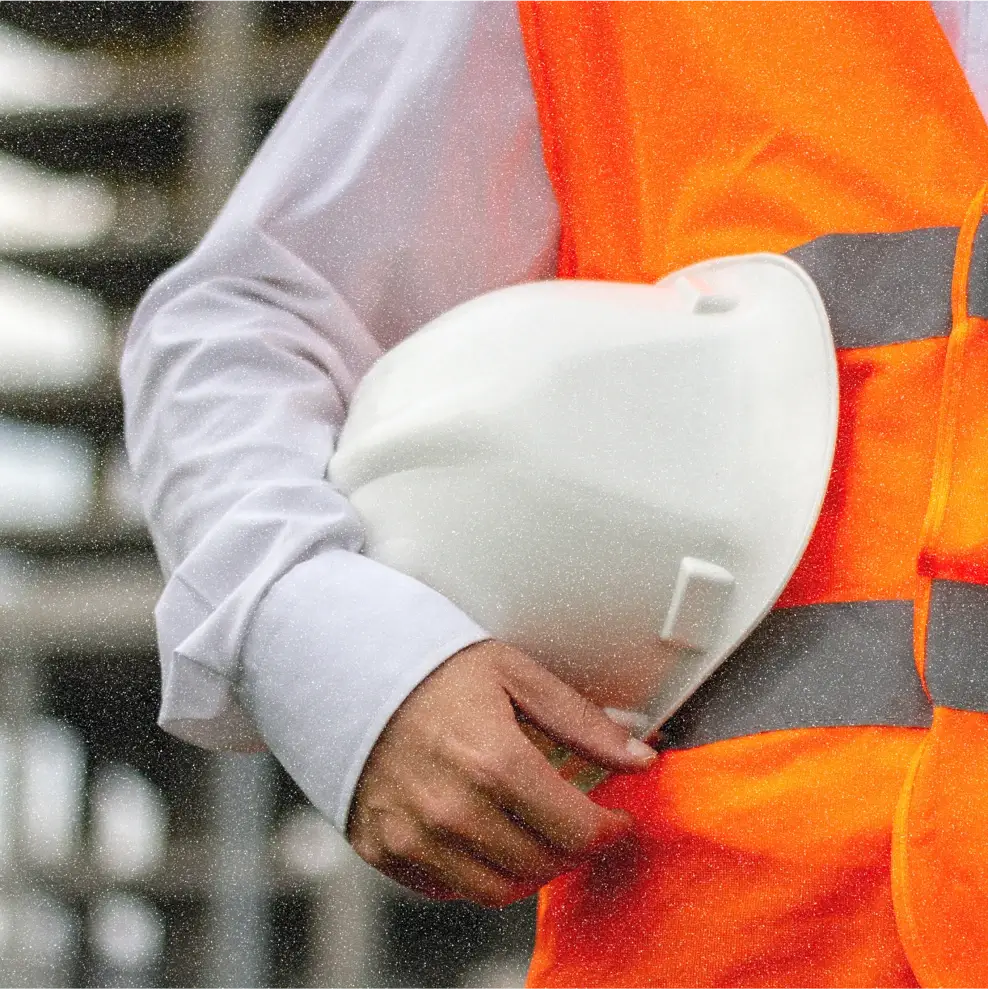
Keep Incidents Low
& Productivity High
A safe workplace reduces disruptions and helps keep moral high. Ensure your employees are equipped to prevent injuries on the production line through our safety training and consultation.
"Manufacture Nevada is great to work with, and they have been a very good resource for not only our continuous improvement initiatives but also for networking referrals resulting in collaborative problem-solving.”
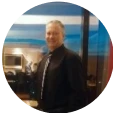
Take the First Step
Get in contact with a Manufacture Nevada representative to discuss
reaching your growth targets.